- 2025 Jan 23
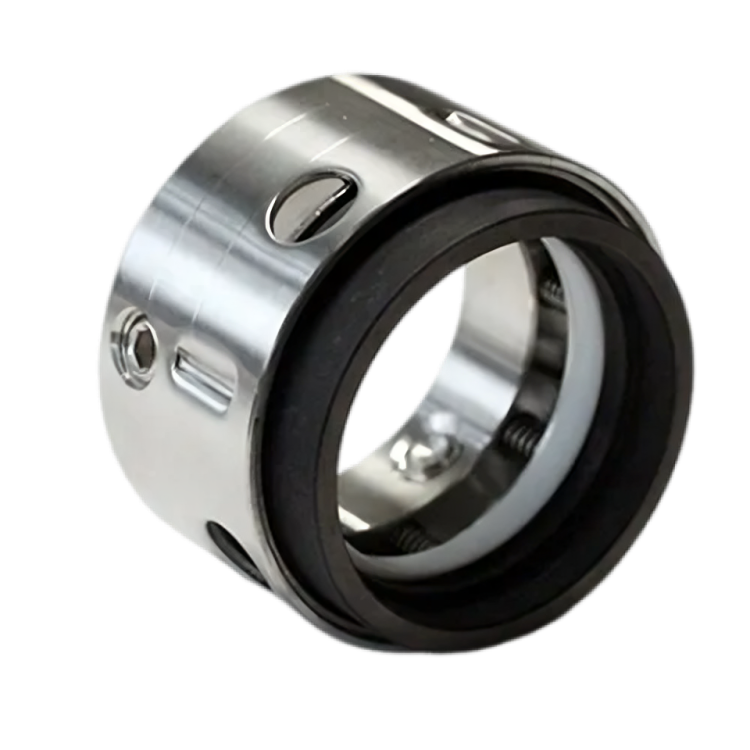
mechanical seal
c mechanical seal mechanicalal mechanical seal mechanical sealTo select a suitable mechanical seal or seal, there are many important conditions that the technical department of factories must pay attention to. Among the important things in the mechanism of mechanical seals is the fluid or sealed materials in the system, which themselves have different groups such as liquids, gases, semi-solids and solids, each of which has its own subgroups and each of which requires conditions for selecting a mechanical seal. Of course, the materials that make up the mechanical seals themselves must be selected in a specialized manner and in accordance with the conditions of the pump and the environment, as well as the fluid, which can be made up of several metal, carbon (mechanical coal), elastomers and O-ring parts, which are also called coal seals. Today, leaks in systems are unacceptable and we must use suitable and high-quality mechanical seals to seal tanks and pumps. In this article, we will examine the conditions of a mechanical seal or mechanical seal in more detail to determine the importance of using this component in the industry and also coal seals
To make a better choice in determining the appropriate type of mechanical seal, the following points should be considered:
1. Grouping the sealing fluid into the appropriate group
2. Specifying the appropriate sealing material
3. Applying sensitive environmental controls when necessary
1. Sealing fluid grouping
To seal the various chemicals used in industry, the chemicals available must be grouped so that the appropriate components can be used in the sealing system for each group. Each fluid can be grouped as a liquid or gas and placed into seven sealing groups. These seven groups are:
1. Fluids that are sensitive to slight changes in temperature and pressure
2. Fluids that require two mechanical seals
3. Non-oily fluids such as gases and solids
4. Slurries
(included in the solid-in-liquid group and may contain abrasive solids.)
5. Fluids that are sensitive to movement
6. Fluids that react with each other to form solids
7. Oily fluids
Now we will examine these groups in detail to understand their effects on the mechanical life of the seal
1-1. Fluids that are sensitive to slight changes in temperature and pressure
Any fluid can be affected by large changes in temperature and pressure, but many fluids are sensitive to small changes in temperature and pressure.
A small change of one atmosphere of pressure (one bar or 15 psi) and 10 degrees Celsius (18 degrees Fahrenheit) in temperature is considered to be a change in temperature. These numbers were chosen because the best mechanical seal designs can produce this temperature difference between the mating surfaces. A mechanical seal can have a pressure drop of one atmosphere across the mating surfaces
• Corrosive fluids that are sensitive to temperature increases. Their corrosion rate doubles with an increase in temperature of 18 degrees Fahrenheit (10 degrees Celsius). The temperature at the seal surface is always hotter than the temperature recorded in the seal chamber. Remember that any contact between the rotating shaft and the stationary part will cause excessive heat and will be considered localized corrosion in a mechanical seal. Wear rings and annular discs are the cause of this type of wear
• Most liquids evaporate when heated or when the seal chamber pressure is greatly reduced. The problem is the low specific gravity product. If the product evaporates between the polished seal surfaces, it will cause the surfaces to separate, just as gases do by expanding. When hot water evaporates, some chemicals are left dissolved in the water. Most of these chemicals remain as hard crystals that can damage the polished surfaces of the mechanical seal
• Fluids such as benzene, etc. with specific gravity that freeze when vaporized, and if they are placed on the surface of the seal, oil or some kind of lubricant, these materials will also freeze and cause damage to the polished surfaces of the mechanical seal. Moisture on the outside of the mechanical seal may also freeze and cause restriction of the sliding and bending movement of the mechanical seal parts
• Some of these liquids solidify as the temperature increases, and others solidify as the temperature decreases. Solvents evaporate at low pressure, leaving behind solids. Paint is a good example of this because in this case, the solvent evaporates at atmospheric pressure or below. In most cases, information about the evaporation time of the solvent or carrier can be obtained by consulting a vapor pressure table
• The adhesion of viscous products decreases with increasing temperature and increases with decreasing temperature. Among fluids, oil is a good example of this. High adhesion can affect the movement of the moving surface of a mechanical seal and cause the sealing surfaces to separate, and lowering the adhesion increases the wear of the sealing surface because the film thickness is not enough to keep the surfaces apart. In this case, a film with a thickness of at least one micron (0.000039 inches) is required to keep the polished mechanical seal surfaces apart
Liquids that cause film formation include:
1. Petroleum products form a kind of oil paint due to the initial heat and then form a layer of coke as the temperature increases. These changes are not reversible and the product formed, which is a hard film, limits the sliding and bending movement of the mechanical seal parts
2. Hard water is another example of a fluid that causes film formation
3. Hot water systems remove magnetite (iron oxide) from the inside of the pipes. This material is black or red in color and is also attracted to magnets. This abrasive material collects on the mechanical seal parts and damages the dynamic O-ring. It also restricts the movement of the mechanical seal and causes the polished surfaces to open. Magnetite is a serious problem for new hot water systems. However, this problem also resolves over time as the system ages and the protective film hardens.
• Liquids that crystallize (salt and sugar solutions) can cause carbon damage if the crystals form between the surfaces. If the crystals form on the sliding and flexural parts of a mechanical seal, the seal surfaces will open as soon as the shaft moves. Any leakage through the seal surfaces will cause solids to form on the other side of the mechanical seal surfaces, thereby interfering with the movement of the mechanical seal as it balances out surface wear
The names of the chemicals are not very important. If you know how to seal one of these materials, you can actually seal all the others. So it is best to put the given chemicals in the correct group and know how the chemicals in that group seal
The pressure or temperature of the product created within the seal enclosure must be controlled to avoid the problems mentioned above. In most cases, the use of two hard surfaces should be avoided, as excessive heat is generated between these surfaces due to the high friction. Only mechanical seals that are hydraulically balanced are acceptable at any temperature and pressure for the sensitive fluid
2-1. Fluids that require two mechanical seals
These mechanical seals are installed with a flow of barrier or buffer fluid between the mechanical seals. If the fluid pressure is greater than the pressure inside the mechanical seal chamber, it is called barrier fluid, and if the pressure is less, it is called buffer fluid. The pressure of the barrier or buffer fluid can be adjusted to indicate any problems in either mechanical seal and allow the pump enough time to stop
• Valuable products fall into this category. Sometimes the products are so valuable that the user will not allow these materials to leak
• Hazardous products that require mechanical seals. These types of fluids fall into a special category because the smallest amount of leakage from this category is not acceptable, the danger of this category may also extend to other categories such as radiation, poisoning, fire, explosion, the presence of microbes, etc
• Pollutants also fall into this category. In general, too much or too little leakage of pollutants is not at all pleasant. In this day and age, no responsible company would allow pollutants to leak into the air or ground for any reason
• Any unexpected seal failures are caused by improper mechanical seal pairing. In many plants, the time lost is valuable. Two seals prevent unexpected seal failures
3-1. Sealing of non-oily materials
The important points of this category are as follows
• Non-oily fluids such as solvents and hot water fall into this group. Very rapid surface wear is experienced with these types of fluids. In most cases the film thickness is less than one micron and as a result the mechanical seal cannot withstand the load created between the sliding surfaces
•Dry gases, which are more of a problem than non-oily liquids. These gases, unlike non-oily liquids, do not conduct heat well and are also dangerous. If you forget to place the seal housing outside a vertical pump, the above problem becomes a common problem. Another example of this is a mixer with an inlet at the top
•Dry solids, which are the main problem. These types of solids cause the sliding parts of the mechanical seal to become compacted, thus preventing the mechanical seal surfaces from lubricating. When the surfaces are open, these types of solids penetrate between the polished surfaces, thus damaging the polished surfaces. For this group, we can mention pharmaceuticals, packaged dry coffee, cake mixes
4-1. Grouts
Another sealing problem is slurries, especially abrasive slurries. Like dry solids, they can cause the mechanical seal parts to become compacted and cause surface damage. These materials collect on the sliding and flexing parts of the mechanical seal, causing the surfaces to open up, then penetrate between the polished surfaces, causing surface damage and leakage. In many mechanical seal designs, the spring or accordion seals (metal or elastomer) wear out rapidly in a short period of time. In these designs, the important thing is to have the fluid rotate with the mechanical seal, not the accordion part of the mechanical seal rotating in the abrasive slurry
5-1. Fluids that are sensitive to movement
These materials can have low or high adhesive properties inside the pump's mechanical seal chamber
• Expansion with movement increases the viscosity of these fluids. Some clay slurries have this problem, and as a result, the high viscosity limits the free movement of the mechanical seal
• The movement of gelatinous fluids reduces the viscosity of these fluids. These fluids rarely cause problems for mechanical seals, but they do increase wear on the mechanical seal surface
•The movement of plastic fluids causes a sudden change in the viscosity of these types of fluids. Sauce (ketchup and mushroom sauce) is a good example of this type of fluid
• The movement of Newtonian fluids does not change the viscosity of these fluids, unless they are classified in another group, in which case they do not cause any problems for mechanical seals
6-1. Liquids that combine with each other to form a solid
We rarely have problems with these types of fluids in pumps because the mixing is done outside the pump, but sometimes problems arise in mixers. Remember that fluids that solidify in the absence of air (anaerobic) are not included in any group
(The first product that comes to mind is super glue.)
• Epoxy is a combination of resin and hardener
• Combining several liquids together forms the plastic material Styrofoam
7-1. Oily liquids
These types of fluids are best used in mechanical seals. While we rarely see this type of fluid used, most of the time we are not sealing the unfinished product to fit into one or more of the above groups. In the past, when packing was used in pumps, this group was not considered at all because it would have allowed the product to leak onto the ground or we would have washed the leaking material with clean fluid and focused more on sealing the clean flow
2- Thematic review of heat transfer oil
Nowadays, leakage of many materials is not tolerable and desirable, and in order to be able to perform the sealing work more effectively, you must have sufficient knowledge of the chemical groups mentioned. In many of these cases, it is also possible that the sealing fluid falls into several of the groups mentioned. For example, when using heat transfer oil, this material falls into the following five groups, which are:
♦ Hot Materials
This type of oil is pumped at temperatures of 600-700°F (315-370°C) and the fluid is too hot for existing elastomers
♦ The film forming material
of the product created at these temperatures is converted to charcoal
♦ Hazardous substances
You don't need such oil that has high temperature and leaks outside. This type of oil is not only a fire hazard, but also dangerous for the user. Recent information shows that some of these oils are also in the group of carcinogenic substances.
♦ Expensive materials
The price of many transmission oils is high
♦ Slurry:
Solid materials are also present in this group due to charring
To be able to perform the heat transfer oil sealing operation well, you must consider all the problems mentioned. When working with all slurries, you must recognize the following problems such as vibration (if the impeller is unbalanced), heat build-up, and if using open impellers, you must know the typical impeller settings.
Evaluation of pump operating conditions
In addition to the use of various chemicals, there are many harsh operating conditions that affect the selection of the appropriate mechanical seal. These operating conditions are divided into seven groups, which are:
1- Hot products
The term superheat includes its application to one of the mechanical seal components, or the amount of heat sufficient
to cause the fluid to change from a liquid to a gas or solid. The best example for this group is heat transfer oil, which is a fluid that turns to coal at high temperatures.
2- Refrigerant fluids
These types of fluids are problematic for elastomers and carbon surfaces. Examples of this group include liquid nitrogen or oxygen
3- High pressure
Includes pressure exceeding 400 psi (28 bar) for the seal chamber, pipelines, boilers and rotary pumps can have this pressure defined for the seal chamber
4- Low vacuum
This includes pressures of 0.01 torr or lower. This low value is also suitable for evaporator and condenser applications
5- High speed
Mechanical seals are classified as high speed pumps if they move at speeds greater than 5,000 feet per minute (fpm) or 25 meters per second. Most pumps manufactured do not have this speed. However, the Sun dyne (Sundstrand) pump is designed for high speed applications
6- Too much movement
It is used for movement of more than 0.005 inch (0.15 mm) in the radial or axial direction. Shaft movement in mixers, actuators, and special components reaches up to 11.8 inches (3 mm). Examples of this group include vertical pumps with long shafts and pumps equipped with sleeves or spherical bearings
7- High vibration
Unfortunately, there are no acceptable numbers for the vibration limit of mechanical seals. Most vibration studies have been done only on bearings. It is worth noting that excessive vibration can cause the following problems:
► Causes the polished surfaces of the mechanical seal to open
► Cause the outer diameter of the carbon surface to crack
► Causes the accordions used in some mechanical seal designs to break
► Causes wear on the drive mechanism, which transmits torque from the locking screws to the mechanical seal surfaces
► Causes movement screws to loosen
► Reduces bearing life
► With more vibration, mechanical seal designs can damage (cause wear) expensive mechanical seal surfaces and shafts
► Most, but not all, mechanical seal designs are built in vibration-damping conditions to mitigate some of the above problems